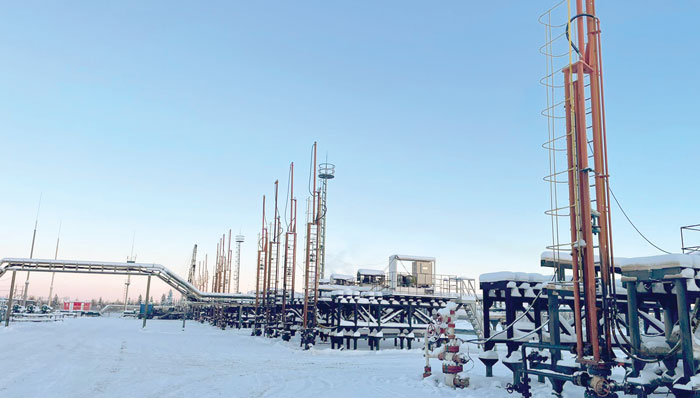
Нефть пермокарбона на крупнейшем в Республике Коми Усинском месторождении неслучайно называется тяжелой. Она высоковязкая, что требует применения особенного оборудования. Нефтяники ЛУКОЙЛа постоянно в поиске новых методик в добыче этих запасов. Об одной из технологий, заключающейся в использовании штанговых насосов без перехода на промежуточный способ добычи винтовыми насосами, «СВ» рассказал ведущий технолог отдела добычи нефти ТПП «ЛУКОЙЛ-Усинскнефтегаз» Айрат Зиянгулов.
– Разработка Усинского месторождения, запасы нефти которого оцениваются в сотни миллионов тонн, является одним из приоритетных проектов ПАО «ЛУКОЙЛ». Месторождение характеризуется карбонатными отложениями, залегающими на глубине 950–1 500 метров, неоднородностью строения и фильтрационно-емкостных свойств, но главное – аномально высокой вязкостью нефти.
Для понимания: сверхвязким считается черное золото вязкостью свыше 200 миллипаскалей на секунду (мПа × с), но этот показатель на пермокарбоновой залежи составляет аж 710 мПа × с. Нефть пермокарбоновой залежи относится к трудноизвлекаемым запасам.
Основная проблема разработки залежи заключается в том, что естественные температурные условия не обеспечивают необходимой подвижности нефти во время фильтрации по пласту и притоку скважины. В связи с этим для увеличения нефтеотдачи применяются тепловые методы воздействия на пласт: площадное паротепловое воздействие (заводнение паром), паротепловая обработка (пароциклическая обработка – ПЦО) и закачка пара в системе горизонтальных скважин (парогравитационный дренаж пласта – ПГД).
ПЦО – самая распространенная технология для пермокарбоновой залежи, ее суть заключается в циклическом использовании одной скважины в качестве нагнетательной и добывающей. Для снижения вязкости производится закачка пара в пласт с помощью блочных парогенераторов в стационарном или мобильном исполнении (процесс занимает от одного до трех месяцев). После прекращения закачки пара происходит термостабилизация (в среднем семь суток), после чего скважина переводится в режим эксплуатации. Для добычи нефти после паровоздействия применяются стандартные штанговые насосы, так как высокая температура жидкости не позволяет эксплуатировать насосное оборудование с погружным электродвигателем. После того как температура жидкости снижается, эксплуатация скважины переводится на насосы с электропогружным двигателем.
Для оптимизации процесса ПЦО в отделе добычи нефти и газа ТПП «ЛУКОЙЛ-Усинскнефтегаз» была внедрена альтернативная технология, разработанная совестно с машиностроителями (компаниями ООО «ЭЛКАМ» и АО «Кубаньнефтемаш»). Ее суть заключается в цикличном осуществлении закачки и увеличении времени эксплуатации добычи с помощью штангового насоса (ШГН) без перехода на промежуточный способ добычи винтовыми насосами (ШВН).
Комплекс включает в себя оборудование в термостойком исполнении – арматура АТПК, труба в термокожухе ТТ-114, специальный ШГН типа СПР (с механическими уплотнениями на плунжере и всасывающем клапане, температура эксплуатации до 400 °С) и термопакер. В качестве наземного привода используется станок-качалка либо гидравлический привод.
Как это работает
Первым этапом производится подготовка скважины к обработке и закачка теплоносителя: на протяжении одного-двух месяцев осуществляется подача пара в пласт с помощью парогенераторов. После закачки расчетного количества теплоносителя в пласт скважина останавливается на термостабилизацию и разряжается. Затем совершается подготовка скважины к эксплуатации: с помощью подъемника или крана производится посадка плунжера насоса СПР в цилиндр. Вызывается подача, и скважина переводится в режим добычи. После окончания эффекта цикл повторяется.
В период с декабря 2019-го по март 2020 года внедрили семь компоновок с насосами СПР и термооборудованием. В ходе эксплуатации были выявлены ограничения этой технологии:
- Осложненный вывод скважины на режим (ВНР), зависание штанг при запуске скважины, длительное расхаживание штанг с помощью станка-качалки в ручном режиме. Для исключения этого осложнения необходимо привлечение автокрана для демонтажа СУСГ (сальника устьевого с самоустанавливающейся головкой) и ПШ (привода штангового) и кратковременная подача пара или прямая промывка в НКТ горячей нефтью с помощью АДПМ (агрегатов для депарафинизации скважин).
- Исключена возможность промывки глубинно-насосного оборудования (ГНО) через затрубное пространство в случае зависания колонны штанг в процессе эксплуатации.
- Влияние газа. Отвод газа из подпакерного пространства возможен только при подрыве плунжера из корпуса насоса СПР с привлечением автокрана, что несет дополнительные затраты.
- Ограничение длины хода станка-качалки до трех метров, ввиду конструктивных особенностей (большой высоты), термостойкой фонтанной арматурой АФК с имеющимся свайным полем станка-качалки.
- Отсутствие возможности проведения ГИС (термометрии) ввиду конструктивных особенностей и малого проходного сечения насоса СПР.
- Коррозия ГНО в связи с невозможностью подачи ингибиторов в подпакерное пространство.
Таким образом, с учетом полученного опыта эксплуатации и осложнений машиностроители доработали компоновку оборудования: станок-качалка заменен на гидравлический привод с длиной хода до четырех метров со скважинным модулем, проведена доработка конструкции универсальной термостойкой арматуры для монтажа гидропривода, разработано два варианта переходной станины для установки гидропривода на арматуру, выполнена конструкция устьевого сальника в термостойком исполнении до 350 °С, заменен термопакер на гидравлический с газоотводом и в компоновку добавлен протектор коррозии, который подвешивается под насос СПР.
Благодаря замене станка-качалки на гидропривод исключаются сложности при ВНР скважины за счет возможности в ручном режиме извлекать плунжер из насоса и производить прямую промывку в НКТ от АДПМ или кратковременно подавать пар. Использование высокотемпературного СУСГ с герметизацией полированного штока позволило проводить пароциклические обработки без его демонтажа и привлечения автокрана или бригады капитального ремонта скважин.
В результате совместных доработок и внедрения этой технологии удалось оптимизировать процесс пароциклической обработки, снизить текущие затраты и исключить влияние осложнений и ограничения, выявленные в ходе эксплуатации.
Подготовила
Светлана БЫКОВСКАЯ